Update: Manufacturer Maintenance Agreements
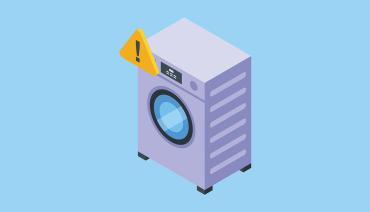
CHICAGO — In today’s business environment of labor challenges and higher costs, laundry operations need to keep their equipment running at peak performance.
One way to do this is to take advantage of manufacturer maintenance agreements.
Patrick Gittard, marketing manager for JENSEN USA Inc., defines these agreements as “when a laundry enlists the support of the manufacturer to help with maintenance of their equipment. It can vary in frequency and involvement.
“On a basic level, it could be a yearly inspection of each machine to perform preventative maintenance and offer recommendations of necessary service and/or replacement parts.”
American Laundry News reached out to laundry equipment manufacturers throughout the industry to find out if and how these agreements have changed over the past few years.
Besides Gittard, representatives who took part were Sandro Bortoloni, director of aftermarket services for G.A. Braun; Jim Shaw, vice president and national accounts sales manager for Lavatec Laundry Technology; and Douglas Konke, head of service U.S., regional service director NAM region, for Miele Professional.
BORTOLONI: Today’s business climate has forced a change from reactive maintenance to scheduled maintenance. Employee turnover and more energy and resource-conscious operators have driven this need.
Laundry operators are demanding reliable, strong, and durable equipment and processes.
GITTARD: We see the trend of laundries wanting more maintenance support both in terms of frequency as well as support in troubleshooting problems that may occur.
SHAW: Our industry, like most service industries, is experiencing a shortage of qualified technicians and engineers.
Many manufacturers offer schoolroom training, but by utilizing a manufacturer’s maintenance agreement, the customer’s technicians stay on site for emergencies and receive “hands-on” training opportunities with their equipment.
KONKE: The demand for maintenance agreements has increased as companies look to optimize their equipment and operations.
Manufacturer maintenance agreements provide regular service of laundry equipment to ensure optimal performance and minimized downtime, but their details can vary depending on location, market demand and specific company policies.
BORTOLONI: Our program has not drastically changed over the past few years as we believe we have a proven proactive program that includes non-destructive testing, periodic inspection, pre-planned maintenance procedures, and maintenance to correct issues found during testing and inspection steps.
GITTARD: For us, I wouldn’t say we have changed any of the fundamental terms or features, but we do see a trend of laundries having trouble hiring their own maintenance technician(s).
For most laundries, proper maintenance of solutions isn’t something that can be compromised, thus we are seeing greater interest in maintenance agreements.
SHAW: All agreements should change to meet their client’s evolving needs, whether it is related to time frames, payments or something along those lines.
KONKE: Maintenance agreements for laundry equipment manufacturers have evolved over the past few years due to advancements in technology, increased competition, a stronger focus on equipment customization, stronger environmental regulations and customer feedback.
Overall, manufacturers aim to provide agreements that offer customers value, reliability and flexibility in a competitive market. With that in mind, we have seen more flexibility with agreements to ensure alignment with the customer’s specific application and usage.
For example, machines used during multiple shifts throughout the day may need additional maintenance versus equipment that is only used a few hours a day.
BORTOLONI: Our programs consist of lubricating, adjusting and providing minor component replacement to extend equipment life.
GITTARD: The main variable is frequency.
SHAW: Most of the terms I have been involved with relate to the timeframes that greatly depend on the demands of the facility. They start out as monthly visits before switching to quarterly, and then moving on to become semi-annual.
KONKE: Standard terms for maintenance agreements typically include scheduled maintenance visits, parts replacement, coverage of labor costs, emergency services for equipment breakdowns, technical support, and service reports and documentation.
Additionally, depending on the manufacturer and the specific needs of the customer, some manufacturers may include unique terms like remote monitoring, predictive maintenance, extended warranties, discounts, training programs and customized service plans.
Agreement terms usually allow for maintenance once a year or every thousand hours of operation, while unique terms may include monthly maintenance or additional parts replacement related to unexpected wear.
BORTOLONI: The benefits of our maintenance agreements include:
- Asset value preservation.
- Improved/minimized energy usage.
- Improved safety and quality conditions.
- Increased capacity and throughput.
- Reduced equipment downtime.
- Refresher training for operations team members.
GITTARD: Maintenance agreements allow a laundry the peace of mind that the equipment is operating to the best of its potential and there isn’t some unknown issue impacting production efficiency.
Also, for a laundry that can’t find technicians, their local staff may not have the experience to perform in-depth troubleshooting on the production line, so they gain the value of having highly experienced technicians visit the laundry.
However, even larger laundry groups with large maintenance teams see value in the manufacturer looking at the solution and making sure that it is performing like it should.
SHAW: As I mentioned, the benefits relate to the training of the plant engineers on their specific equipment and setting up the time intervals that yield the best results.
KONKE: The best maintenance agreements maximize the equipment’s uptime and performance through regular checks that ensure proper operation and identify potential issues before they become a problem—helping to ensure customers are receiving the best return on their investment.
Other benefits of these agreements include:
- Extended lifespan: Proper maintenance prolongs equipment lifespan and cuts repair costs.
- Priority service: Operators receive prompt assistance during emergencies or peak times.
- Access to expertise: Trained technicians offer specialized knowledge for using equipment.
BORTOLONI: We believe our customers take advantage of our maintenance agreements and effectiveness stems from our use of our factory-trained service technicians, ensuring top-notch expertise, along with the assurance of genuine factory-certified replacement parts (no third-party involvement, only the equipment manufacturer).
GITTARD: Our customers mainly take advantage of the trained eye of our JENSEN technicians, including the recommendations for necessary service to be performed and recommended repair parts.
SHAW: It appears that most service agreements begin as monthly visits and then evolve into quarterly agreements.
The reason is apparent: the site technicians no longer need the repetitive training.
KONKE: In my experience, most customers typically take advantage of at least the minimum recommended preventive maintenance visits, similar to recommended oil changes for your car.
Laundries frequently utilize these visits to ensure their equipment operates efficiently and reliably. By proactively addressing maintenance needs and having access to timely support, laundries can maintain smooth operations and continue delivering high-quality services to their customers.
GITTARD: The customers who are using our maintenance programs are taking full advantage of what we offer.
SHAW: There are many facilities that have qualified technicians on staff who are fully capable of performing internal training programs.
KONKE: One aspect of manufacturer maintenance agreements that laundries may not fully utilize is training. Training programs offer valuable opportunities for staff members to enhance their knowledge and skills related to equipment operation and maintenance practices.
Laundries might not take full advantage of these training programs because of time constraints, staffing limitations or a lack of awareness of available training options.
Additionally, some customers opt to cut costs rather than purchase the manufacturer’s maintenance agreement. Unfortunately, that decision could cost more in the long run due to machine downtimes and costly repairs that could have been avoided with regular maintenance.
BORTOLONI: Speak to your equipment manufacturer about customizing a maintenance agreement and training specific to their equipment in your laundry facility. We offer this opportunity to all customers.
GITTARD: Any delay in production can cost money. We have large customers who have extended their contracts for several years.
When we get feedback from customers who perform the analysis between the cost of an occasional maintenance visit and the reduction in risk of production disruptions, the agreements always prove their worth.
SHAW: If there is to be work done with on-site equipment, I recommend having the parts already there prior to the visit so the technicians can optimize the service opportunity.
You may also want to work a parts warranty program into the maintenance agreement.
KONKE: When researching these agreements, think about how frequently you will use the equipment, the likelihood of exposure to harsh substances or chemicals, and your level of redundancy if a machine stops working.
From there, make sure you find a plan that meets the expectations you have for your equipment.
I’d also recommend asking lots of questions. Don’t hesitate to work with manufacturers to better understand any aspects of the maintenance agreement that are unclear. These steps can help laundry operators make more informed decisions when selecting a maintenance agreement to maintain efficient and reliable laundry operations.
Proper maintenance is one of the most important considerations for any piece of equipment you own. If washers and dryers aren’t properly taken care of, it is likely they will have issues down the line that reduce their effectiveness and durability.
We’ve seen equipment last well beyond its expected lifespan simply because it was well-maintained.
Our maintenance plans are focused and flexible to meet the needs of the customer and the equipment. We know our customers use equipment differently and for different purposes.
Our ability to build customizable plans helps ensure their equipment gets the right care at the right times to keep their operations running efficiently.
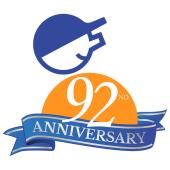
Prudential Overall Supply Celebrating 92 Years
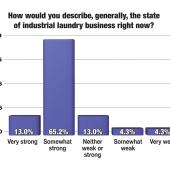
Survey: Most Operators Indicate Laundry Business Strong
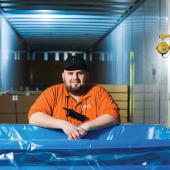
Royal Basket Trucks Earns Workplace Honor
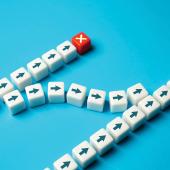
Does Your Independent Laundry Have a Backup Plan?
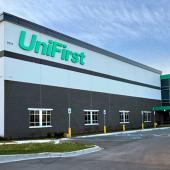
UniFirst Holds Ribbon Cutting for New Michigan Facility
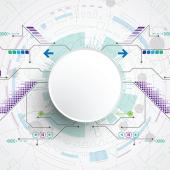
Reliability Training for New Technologies
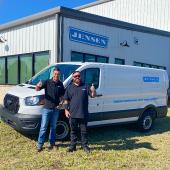
JENSEN USA Launches Fleet of Regional Service Vans
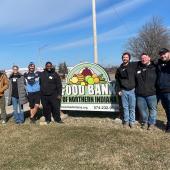
Wildman Employees Provide 605 Service Hours

UniFirst Completes Rooftop Solar Panel Projects
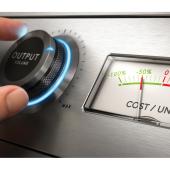
Examining Cost Controls in Laundry & Linen Services (Conclusion)
Podcasts for You
Disaster Preparedness for Laundries
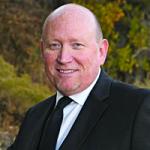
At some point, a laundry is going to face a disaster, at least losing power. In this episode, guest Bob Corfield, principal of Laundry Design Group, talks about ways to keep goods moving during these challenging times.
How Distributor Partners Help Laundry Operations
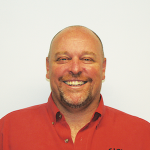
Distributors provide essential equipment to laundry/linen services, but there is more to the equation. Find out more from guest Craig Dakauskas, president of CLEC.
How Social Media Impacts Laundry/Linen Services
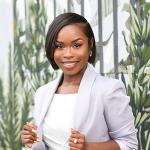
In this podcast, guest Bri Curington, social media director for Infinite Laundry, a marketing agency that works exclusively in the linen and uniform industry, offers help for industrial/commercial and OPL laundries with effective social media strategy.
From the Research Center
Water Recycling in Commercial Laundry

Laundry Design & Construction: Creating the Ideal Workflow
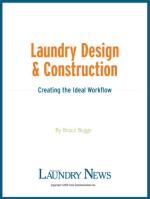
Laundry Chemicals & Dispensing: Finding the Right Chemistry
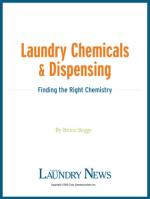
Latest Digital Editions
Digital EditionAmerican Laundry NewsMay 2024
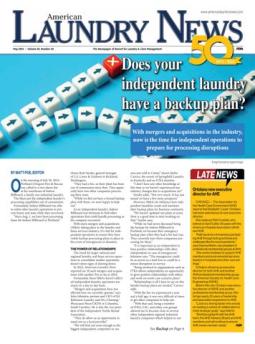
- Does Your Independent Laundry Have a Backup Plan?
- Top 5 Global Robotics Trends in 2024
- Update: Manufacturer Maintenance Agreements
- Panel of Experts: Upping Laundry Brand Game in Marketplace

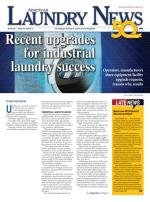