Textiles: Jeffrey Courey, George Courey Inc., Laval, Quebec
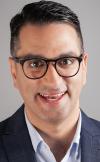
Companies from all sectors need to build more resilient and adaptable supply chains that can withstand unexpected challenges.
Beyond the widespread disruption in global supply chains caused by the COVID-19 pandemic (primarily due to factory shutdowns, transportation restrictions and consolidation of demand on certain products such as PPE and other medical supplies), there were also many other isolated events that have highlighted vulnerabilities in the global supply chain.
For instance, the Suez Canal blockage in March 2021 caused significant disruptions in global shipping routes and prevented over 400 ships from passing through the canal—a major trade route between Asia and Europe.
The increased frequency of extreme weather disasters and ongoing geopolitical tensions like the U.S.-China trade war also contribute to the challenge of finding consistency and security in this era of increasing globalization.
This article highlights some concrete steps that institutional laundries can take to mitigate these risks and ensure they have the necessary supplies to operate, regardless of a potential disruption in their supply chain.
Firstly, it is essential to have a diversified supplier base that focuses on transparent communication and strategic geographical diversification. With these, facilities can stay informed about potential supply chain disruptions and work proactively with suppliers to find solutions.
This can involve exploring alternative sourcing options or adjusting production schedules to accommodate delays or shortages. By spreading sourcing across multiple regions, both customer and supplier can reduce their exposure to an event that is isolated to a certain region.
It is also advisable that laundries invest in data analytics and artificial intelligence technology to gain real-time insights into supply-chain performance to identify potential issues before they become major disruptions.
High-quality analytics use algorithms to predict demand patterns based on factors such as lead time, demand variability and order frequency, which then helps optimize stock levels by minimizing the amount of inventory on hand requirements.
Having efficient demand-planning analytics makes it easier to work with suppliers to leverage vendor-managed inventory (VMI) programs, which in many cases can be an excellent way to improve cash flow and manage physical warehouse space.
While supply-chain challenges remain a real concern for our industry, it is possible for laundries to successfully adapt to these realities by using the array of tools and strategies at their disposal.
By maintaining transparent communication channels with vendor partners, diversifying global sourcing, and leveraging technology to optimize VMI programs and predict potential disruptions, laundries can build resilient and reliable supply chains that can weather any challenges that may arise.
Consulting Services: Cliff Beiser, Champions Touch, Kissimmee, Fla.

The magnitude of these issues can be very regionally based on location and type of laundry business.
Necessary parts for large, older equipment, in particular tunnel washers, and long lead times have been an issue in my local area for more than a decade, yet it serves as a microcosm of the overall supply-chain issues that have been occurring even after the pandemic.
First, research and find everyone who sells the items you are having trouble keeping in stock.
Next, see if there are any alternatives to these items that can be substituted.
Third, speak with the supplier and have a heart-to-heart conversation regarding specific lead times they can “guarantee” their company can live up to.
Additionally, increase your par stock and storage to accommodate the longer lead times that occur currently.
Lastly, and in my case, what worked very well was being friendly with other laundry managers to share needed parts and agreeing to keep extra (high-value) parts for each other and communicating when they are available. We all know how important it is to keep our machines humming and in working order. Below is a bullet point list that I find helpful.
- Expand your supplier list—online business shopping with Amazon Business or even skipping your current supplier and going direct to manufacturer.
- Research alternative products and discuss with your end users (if applicable).
- Speak with supplier regarding specific lead times for each product and adjust your inventory accordingly.
- Increase par stock and storage area to accommodate longer lead times.
- Friendly, ongoing communication with current competitors so you can share with each other.
Equipment Manufacturing: Tom Vanden Heuvel, Kemco Systems, Clearwater, Fla.

As a crucial element in the hospitality, healthcare and industrial sectors, laundry operations must always be ready to function at full capacity.
However, the laundry industry can be affected by various supply-chain challenges, including the availability of critical components, delivery delays, and price fluctuations. As a result, operators must be proactive in securing the necessary components to keep their operations running efficiently.
One way to ensure operators have the required components is to work closely with suppliers. A good supplier will be able to provide valuable insights into the availability of critical spares and provide advice on alternative solutions to potential shortages.
Plant operators can ask their suppliers for recommendations on which spares are essential to keep in stock and which ones they can afford to order when the need arises. By doing so, plants can create a plan of action to mitigate the impact of any potential supply-chain challenges on their operations.
In addition, the maintenance department should be vigilant about the condition of their equipment and the frequency of maintenance checks. By carrying out regular checks, operators can identify any signs of wear and tear on components and replace them proactively before they become critical.
Furthermore, maintenance should have a list of critical components that require more frequent inspections and replacements, such as bearings, filters, belts and motors.
In today’s environment, it is very important to dig your well before you’re thirsty. Be proactive in securing the necessary components to ensure that operations run smoothly.
Working closely with suppliers and carrying out regular maintenance checks can help mitigate potential supply-chain challenges and ensure plants continue to run efficiently.
Click HERE to read Part 1 with ideas from textile/uniform rental and uniforms/workwear manufacturing experts.
Have a question or comment? E-mail our editor Matt Poe at [email protected].